A Comprehensive Overview to the Plastic Shot Molding Modern Technology
Plastic shot molding stands as a keystone of contemporary production, using unparalleled efficiency and accuracy in the production of complex plastic elements. As the landscape of manufacturing evolves, understanding the future trajectory of injection molding ends up being significantly critical.
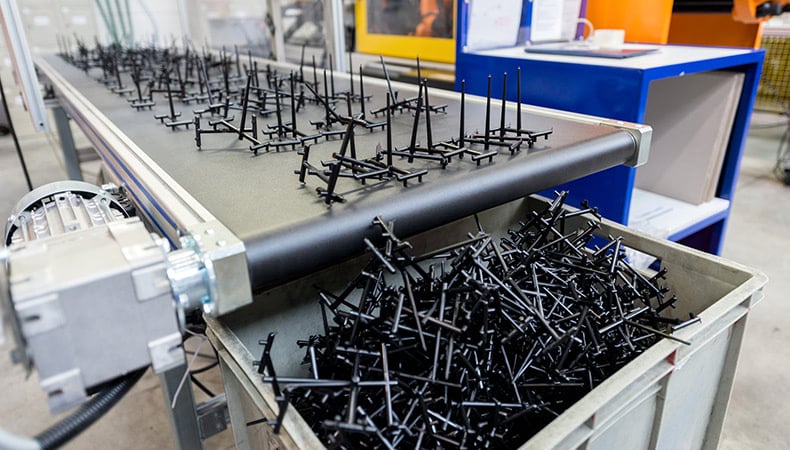
Introduction of Plastic Shot Molding
Plastic shot molding is an extensively used manufacturing procedure that enables the efficient manufacturing of complex plastic components with high accuracy. This innovation has come to be a keystone in different markets, including automobile, customer goods, and electronics, owing to its capability to produce huge amounts of parts rapidly and cost-effectively.
The process includes melting plastic granules and injecting the molten product right into a pre-designed mold and mildew. As soon as cooled down, the mold is eliminated to reveal the ended up element, identified by its complex details and harmony. The adaptability of products used in plastic injection molding, ranging from thermoplastics to thermosetting polymers, enables suppliers to tailor products to satisfy particular requirements, such as strength, resistance, and versatility to warmth or chemicals.
Furthermore, the effectiveness of this method lowers waste and lessens production prices, making it an eye-catching choice for services intending to enhance their production processes. As innovation advances, technologies such as multi-material shot molding and the integration of automation remain to enhance the capacities of plastic shot molding, enabling the creation of significantly sophisticated items that satisfy the needs of modern markets.
The Injection Molding Process
Injection molding is a sophisticated manufacturing strategy that includes numerous critical actions to change raw plastic products right into ended up products. The process begins with the prep work of plastic pellets, which are fed into a heated barrel. Right here, the pellets are melted and co-opted to attain a consistent thickness.
Once appropriately heated up, the molten plastic is injected into a specifically engineered mold under high stress. This action is essential, as it allows the product to load every dental caries of the mold, guaranteeing the end product properly reflects the designated style. The injection time must be thoroughly controlled to stop flaws and make certain reliable material use.
After the mold is filled, it goes through a cooling phase, where the plastic strengthens right into its last form. This cooling process can differ in period depending upon the density and complexity of the part. When cooled down, the mold and mildew opens, and the completed item is ejected.
Trick Advantages of This Technology
One of one of the most substantial benefits of shot molding modern technology depends on its capability to create high quantities of specific and consistent get rid of very little waste. This efficiency stems from the automatic nature of the process, which considerably lowers manual work and the potential for human mistake. As an outcome, suppliers can attain a high level of repeatability in their outcome, making sure that each component fulfills strict high quality criteria.
An additional trick benefit is the versatility of materials that can be utilized in injection molding. A great site variety of thermoplastics and thermosetting polymers can be formed, allowing for tailored residential or commercial properties to fit certain applications. The modern technology supports intricate geometries and elaborate designs, which can be challenging to accomplish with other manufacturing techniques.
Cost-effectiveness is likewise a crucial benefit, specifically for big production runs. The initial investment in mold and mildews may be high, but the long-term cost savings in material waste and labor make injection molding a financially viable option. Finally, shot molding permits for rapid manufacturing cycles, allowing business to react promptly to market demands and lower lead times. These advantages strengthen shot molding's setting as a recommended production procedure across numerous sectors.
Applications Across Industries
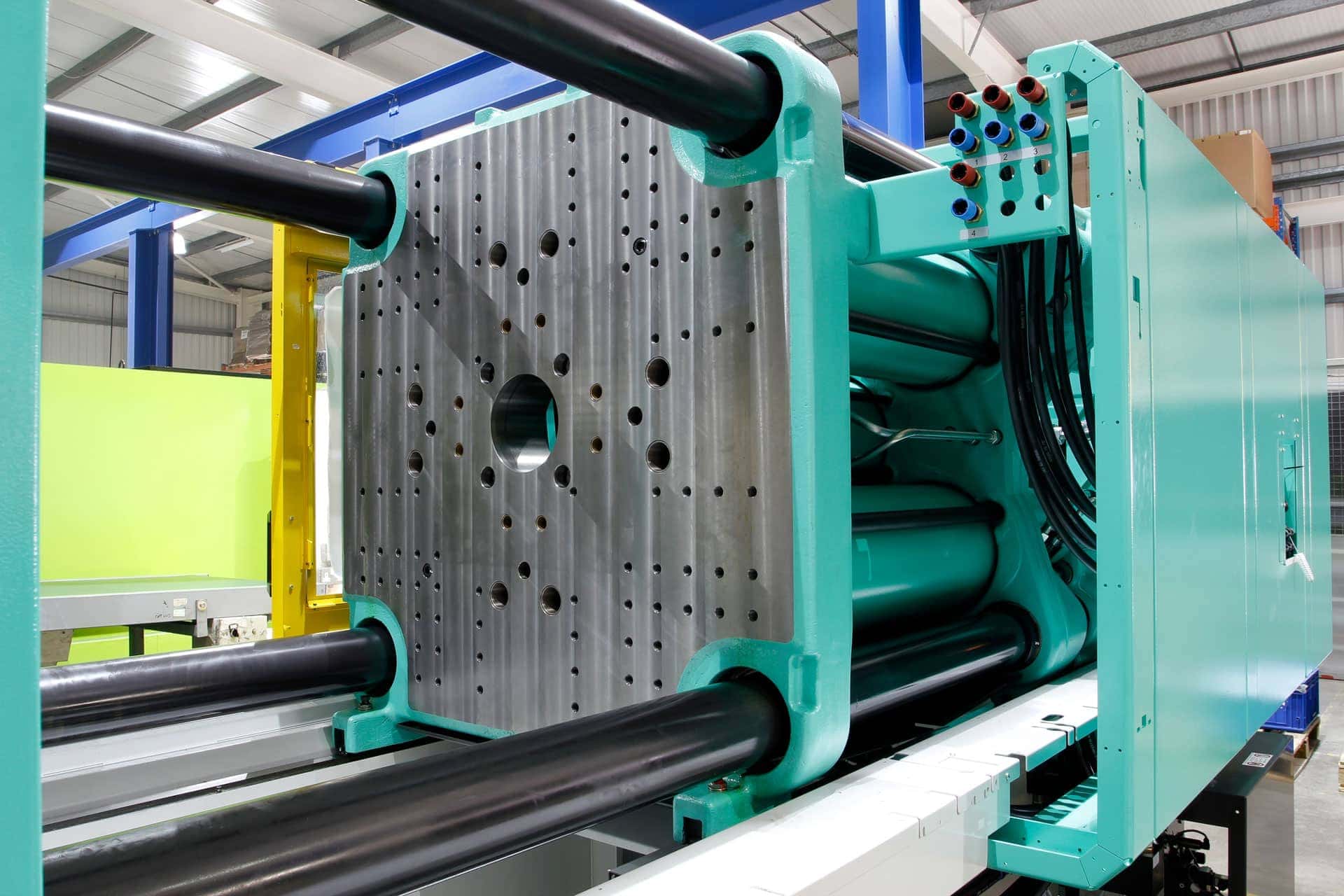
In the clinical field, shot molding is vital for producing high-quality, sterilized elements, consisting of syringes, medical instruments, and housings for medical devices. The capability to preserve tight resistances and produce complicated geometries this content makes it an excellent option for these applications. Moreover, the packaging sector advantages from shot molding by producing a wide variety of containers, closures, and dispensers that are both cost-efficient and reliable.
The toy sector depends greatly on injection you can try these out molding to produce vibrant, resilient, and safe items that interest youngsters. The construction industry makes use of shot molding for generating numerous components, fittings, and elements that contribute to both capability and design. On the whole, the broad selection of applications demonstrates the indispensable duty of injection molding innovation beforehand different markets.
Future Trends in Injection Molding
Accepting advancements in modern technology, the future of shot molding is poised for significant improvement driven by technologies in products, automation, and lasting techniques. Among the most noteworthy patterns is the advancement of bio-based and recycled polymers, which not only decrease reliance on fossil fuels yet also reduce ecological impact. As producers significantly prioritize green services, these materials are coming to be more prevalent in production.
Automation is one more key trend forming the industry. The integration of robotics and expert system into the injection molding procedure improves production, efficiency, and accuracy rate. Smart manufacturing facilities furnished with IoT gadgets permit real-time tracking and predictive maintenance, reducing downtime and maximizing operational procedures.
Additionally, the change in the direction of customized and small-batch production is obtaining momentum. Advanced innovations such as 3D printing and additive production enable quick prototyping and the creation of complex geometries that were previously unattainable. This shift allows firms to respond much more effectively to market demands and consumer choices.
Verdict
In final thought, plastic injection molding technology represents a keystone of modern-day manufacturing, providing efficiency and convenience in producing complex components across varied markets. The comprehensive exam of the injection molding procedure highlights its critical stages and advantages, while the expedition of applications highlights its extensive significance.
Plastic shot molding stands as a cornerstone of contemporary production, offering unequaled effectiveness and precision in the manufacturing of complicated plastic parts (Plastic Injection Molding). The convenience of products utilized in plastic injection molding, ranging from thermoplastics to thermosetting polymers, permits manufacturers to customize products to satisfy particular requirements, such as strength, resistance, and flexibility to heat or chemicals
Shot molding is an advanced production method that entails a number of crucial actions to change raw plastic materials into completed items.The flexibility and performance of injection molding modern technology have led to its extensive fostering throughout various sectors.In verdict, plastic shot molding technology stands for a foundation of modern production, using efficiency and versatility in generating intricate components across diverse industries.